Innovations in Polymer Engineering: Mastery of Blow Molding and Extrusion Technologies
Written by: Steven Guan
Introduction
In the specialized industry of polymer processing, Akei contributes to the ongoing development of high-quality plastic parts through expert blow molding and extrusion techniques. Our focus is on delivering precision and efficiency in the manufacture of diverse products, utilizing advanced blow molding and extrusion technologies and expertise to meet the specific needs of our customers across various industries.
The Essence of Blow Molding
Blow molding is a revolutionary manufacturing process used to create hollow plastic parts. It begins with melting down plastic and forming it into a parison, a tube-like piece with a hole in one end through which compressed air can pass. The parison is clamped into a mold, and air pressure is applied, inflating the plastic into the shape of the mold cavity. This technique is the backbone of industries that require lightweight, durable containers, from everyday water bottles to intricate automotive fuel tanks.
Akei's Advanced Blow Molding Capabilities
Akei’s cutting-edge machinery molding. The company's technical prowess ensures optimal control of variables such as pressure, temperature, and cooling rates, essential for achieving consistent wall thickness and superior part performance. The precision control is done via the
Beckhoff Industrial Computer which provides the highest degree of automation and stability. Akei's equipment is designed for versatility, capable of handling a wide range of thermoplastic materials, and is engineered for both high-volume production and crafting complex shapes.embodies precision and efficiency in every phase of blow.
Single-Screw Extruders: Consistency Is Key
Central to the blow molding process is the extrusion of the parison. Single-screw extruders, a focal point of Akei's technology suite, are the workhorses behind this task. They convert solid plastic granules into a viscous melt by applying heat, pressure, and mechanical shear. The screw geometry is meticulously designed to ensure a consistent and homogenous melt, suitable for forming high-integrity parisons. Integral to the design of these extruders is the L/D ratio, which is the length of the screw divided by its diameter. This ratio is a critical factor in determining the efficiency of the plasticizing process, the quality of the melt, and the throughput of the extruder. A higher L/D ratio typically allows for more residence time in the barrel, enhancing the melting and mixing of the polymer. Akei's extruders optimize this ratio for every project to strike a balance between processing efficiency and melt quality, accommodating a wide array of materials and applications. Advanced features such as grooved feed throats and specialized screw designs further refine the process, ensuring that the extruded parison meets the exact requirements for blow molding applications.
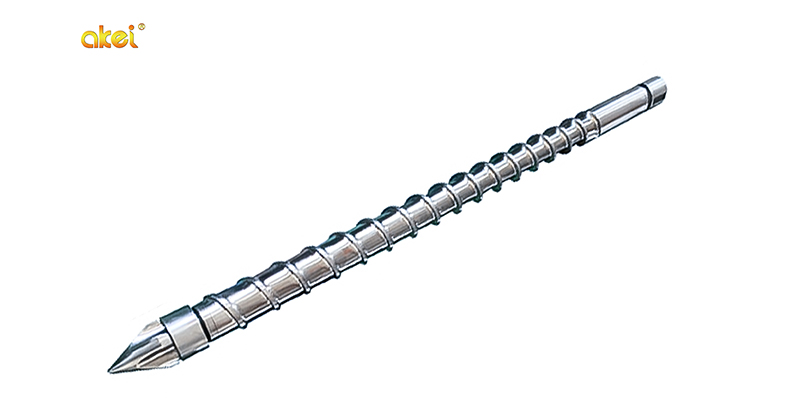
Co-Extrusion: A Symphony of Materials
Expanding upon the capabilities of single-screw extrusion is the process of co-extrusion. This advanced technique allows for the simultaneous extrusion of multiple layers of different materials. Akei harnesses this process to produce multi-layered products, combining the desirable properties of various polymers to meet specific functional requirements, such as barrier properties or UV resistance, while optimizing material costs.
Process Optimization: The Akei Advantage
Akei's commitment to excellence extends to the optimization of the entire extrusion and blow molding process. The company’s equipment features state-of-the-art control systems that ensure precise processing conditions, vital for maintaining product quality and reducing scrap rates. With an eye on sustainability,
Akei's fully electric blow molders is engineered to minimize energy consumption and material waste, contributing to a greener production footprint.
Conclusion
Akei contributes significantly to the polymer processing industry, providing advanced blow molding and extrusion solutions. We are dedicated to crafting high-quality products that fulfill the diverse needs of our clients. For those seeking to incorporate Akei's polymer processing technologies into their production lines, we invite you to
connect with us . Together, we can create solutions that prioritize quality, innovation, and sustainability.
PrevSustainable Practices in Extrusion Blow Molding: Paving the Way for a Greener Industry
NextExtrusion Blow Molding Q&A Information Page