IoT Revolutionizes Extrusion Blow Molding: Akei Is In The Forefront Of This Technological Advancement
Written By: Steven Guan
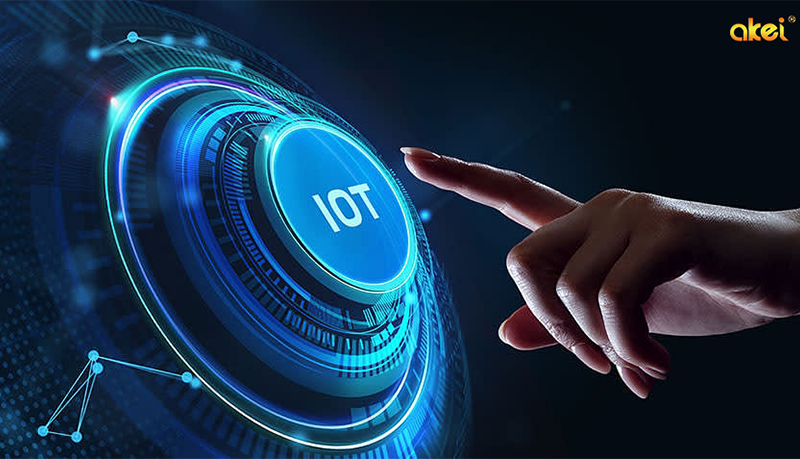
In the ever-evolving landscape of manufacturing, a groundbreaking technological advancement is reshaping the extrusion blow molding industry. The Internet of Things (IoT) has emerged as a game-changer, introducing a plethora of benefits that are revolutionizing the way machines operate, products are manufactured, and businesses compete.
Let's delve into the specifics of how IoT integration is transforming the extrusion blow molding industry:
1. Enhanced Productivity
Imagine a manufacturing floor where machines are not just tools but partners in production. IoT enables real-time monitoring and optimization of machine settings, ensuring they operate at efficiency. This translates into increased productivity and reduced downtime, a winning formula for any manufacturer.
2. Quality Assurance
Consistency is key in manufacturing, and IoT ensures that product quality remains unwavering. Sensors continuously monitor parameters like temperature, pressure, and material flow. Any deviation triggers immediate alerts, enabling operators to take corrective actions promptly. This proactive approach minimizes defects, ensuring products meet quality standards.
3. Cost Reduction
The predictive maintenance capabilities of IoT are a game-changer. By analyzing data from sensors, IoT systems predict maintenance needs, allowing manufacturers to schedul maintenance during planned downtime. This prevents unexpected breakdowns and costly emergency repairs. Additionally, IoT optimizes machine settings for energy efficiency, contributing to cost savings.
4. Remote Management
IoT empowers operators to monitor and control machines remotely, offering unprecedented flexibility. Whether it's adjusting settings or troubleshooting, operators can do it from anywhere, reducing the need for on-site personnel. Operational efficiency reaches new heights.
5. Customization
Manufacturing isn't one-size-fits-all, and IoT understands that. It enables manufacturers to customize machine settings to meet specific production requirements and adapt to different materials. This level of customization enhances versatility, ensuring machines efficiently handle various production scenarios.
6. Resource Optimization
Sustainability is a growing concern, and IoT plays a crucial role. Sensors meticulously track resource usage, including energy and raw materials. By optimizing consumption, IoT minimizes waste and supports sustainability goals, contributing to cost savings and eco-friendliness.
7. Data-Driven Insights
Data is the backbone of informed decision-making. IoT generates a wealth of data that provides manufacturers with invaluable insights. By analyzing historical data, trends and patterns emerge, enabling manufacturers to fine-tune processes, optimize settings, and improve efficiency and waste reduction.
8. Market Competitiveness
In an era defined by smart factories and Industry 4.0, staying competitive means embracing innovation. IoT-enabled machines position manufacturers at the forefront of this revolution. They meet the demands of modern, data-driven factories where efficiency is paramount, attracting customers who value advanced, future-proof solutions.
9. Streamlined Supply Chain
Efficient supply chain management is essential. IoT facilitates seamless communication with suppliers, ensuring just-in-time material delivery. Real-time updates on material availability minimize inventory holding costs, reduce waste, and keep production running smoothly.
10. Safety Improvements
Safety is non-negotiable. IoT sensors monitor safety conditions, including temperature, pressure, and machine movement. When conditions deviate from safe parameters, alarms and alerts are triggered, creating a safer working environment for all.
11. Regulatory Compliance
Meeting industry regulations and standards is a must. IoT data provides a detailed record of machine performance and production processes, simplifying compliance documentation for audits. Compliance not only satisfies legal requirements but also enhances brand reputation and customer trust.
12. Customer Support
IoT unlocks remote access to machine data, a boon for customer support. When a customer encounters an issue, support teams can remotely access machine data to troubleshoot and provide solutions swiftly. Downtime is minimized, and customer satisfaction soars.
In conclusion, the integration of IoT in the extrusion blow molding industry is nothing short of transformative. It empowers manufacturers to optimize productivity, reduce costs, improve quality, and strengthen their competitive position. As Industry 4.0 continues to reshape the manufacturing landscape, those who harness the full potential of IoT are leading the way toward a smarter, more efficient future.
For extrusion blow molding businesses yet to explore IoT possibilities, now is the time to embark on this journey. The future of manufacturing has arrived, let Akei be your partner in this journey.
Prev2021 Chinaplas has come to a complete end. Thank you!
NextThe Evolution of Blow Molding Technology: Past, Present, and Future